Researchers on the College of Cambridge’s Heart for Industrial Photonics have developed a brand new additive manufacturing approach known as laser-assisted chilly spray (LACS). The method combines localized laser heating with a supersonic powder stream to deposit metals and cermets for constructing, coating, or repairing components. This strategy addresses the high-temperature and materials limitations present in comparable methods equivalent to thermal spraying.
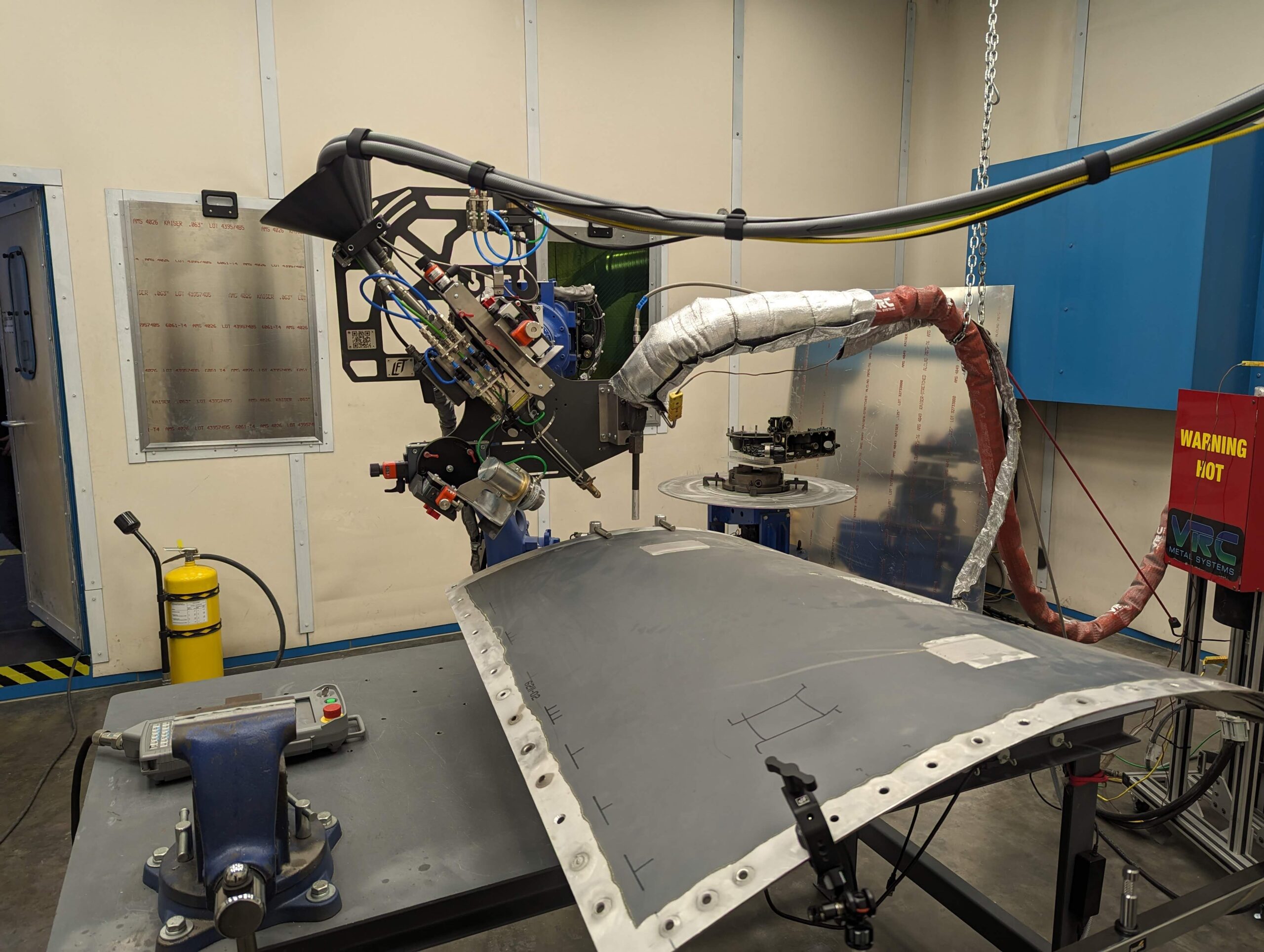
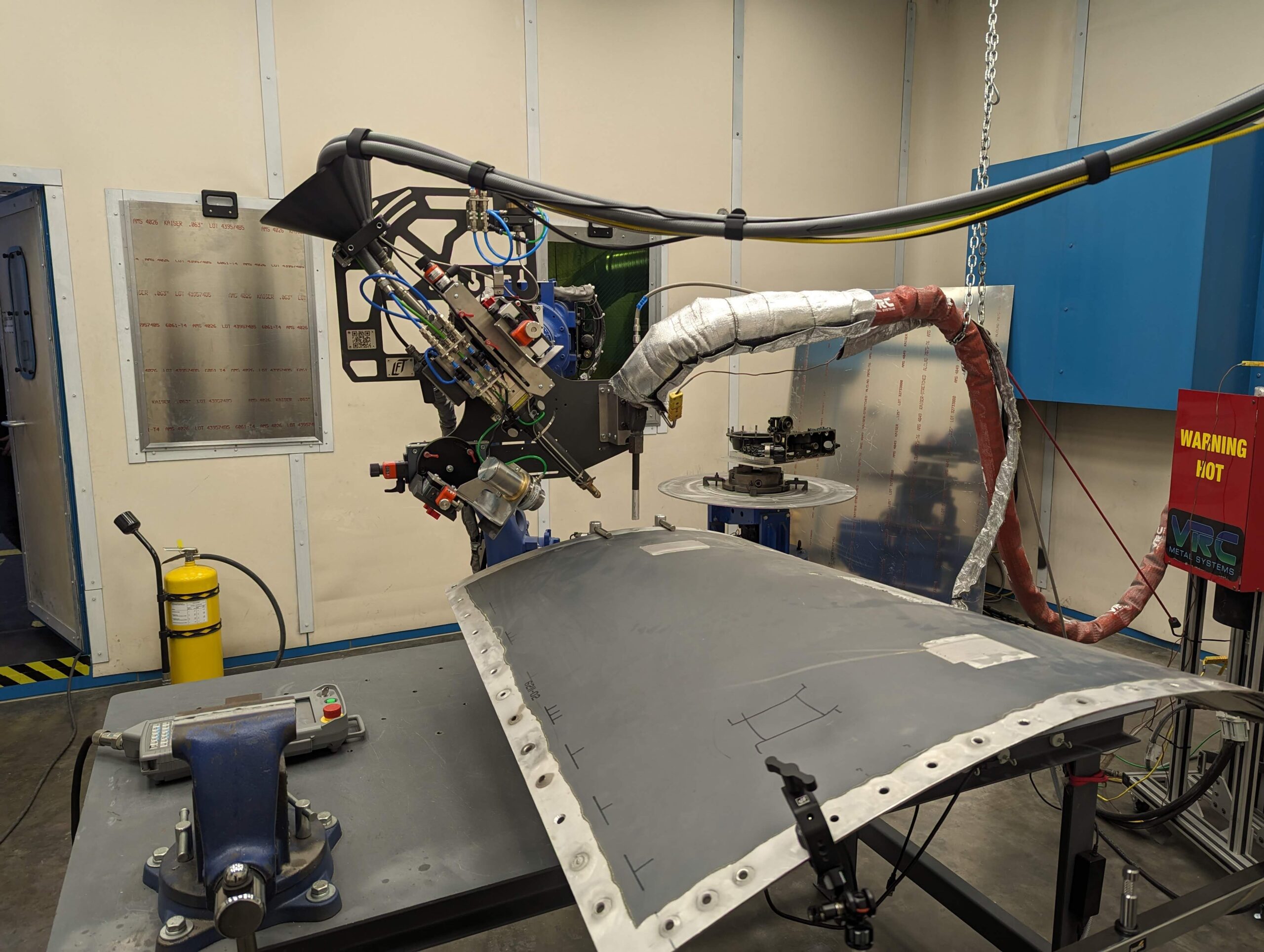
The event addresses a major price problem in chilly spray manufacturing. Conventional chilly spray processes for high-strength supplies like titanium and aluminum alloys require helium as a service fuel, which prices roughly £80 per minute of operation. “The requirement for helium posed a major problem due to its price, which is round £80 per minute of operation. Even state-of-the-art recycling efforts recovered solely round 85% of the helium,” stated Professor Invoice O’Neill, who leads the analysis crew.
LACS gives a number of technical benefits over standard chilly spray strategies. The method allows deposition at decrease particle velocities, which preserves the powder’s construction within the last coating. It additionally operates at decrease fuel temperatures of 400-700°C in comparison with as much as 1,200°C for normal chilly spray, decreasing energy consumption. Coatings may be utilized at charges as much as 10 kg per hour whereas sustaining the substrate under melting temperature to keep away from distortion.
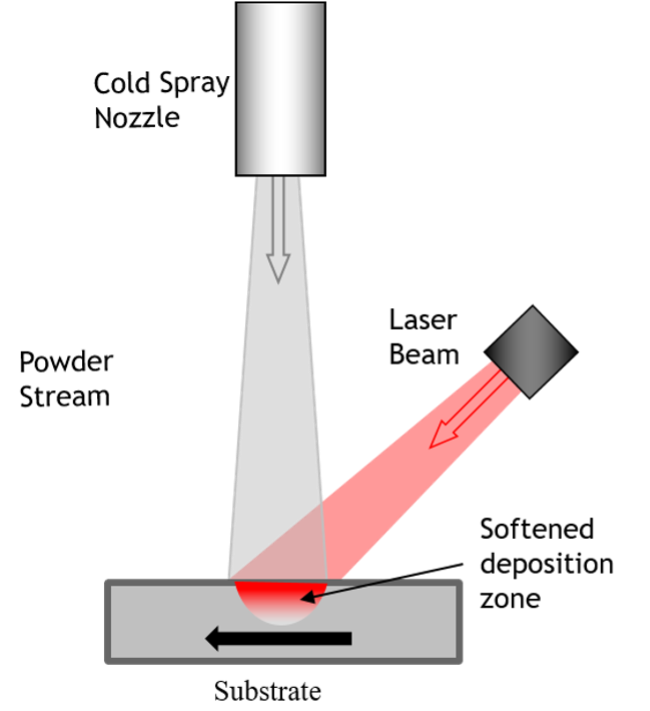
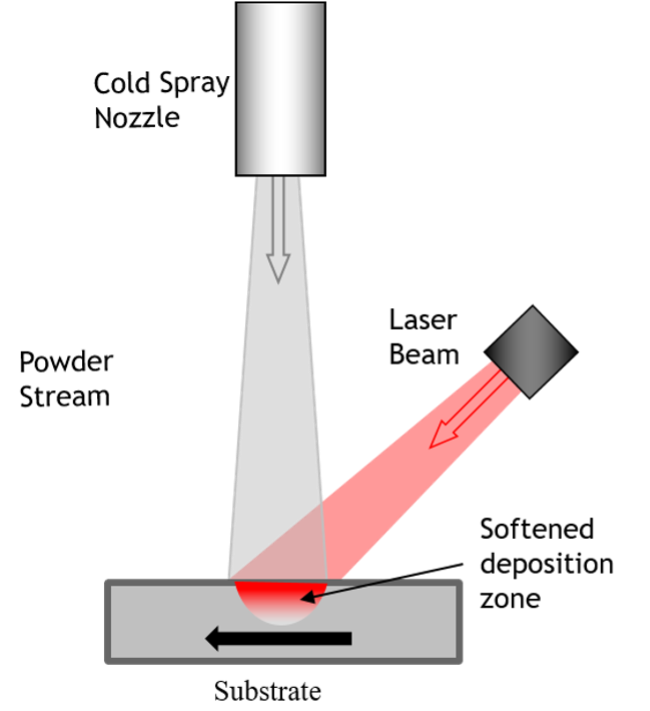
The aerospace business represents a major utility space for LACS expertise. The approach allows on-demand restore and manufacturing of plane parts, doubtlessly extending plane lifespans. Conventional storage of spare components is expensive and space-intensive, and as soon as components are depleted, plane can grow to be unusable attributable to lack of substitute parts. The worldwide additive manufacturing market is projected to succeed in between $70 billion and $88 billion by 2030, with the UK presently holding roughly 7.6% of the worldwide market.
The analysis crew is working to reinforce LACS capabilities for full 3D printing purposes. Present limitations embrace minimal management over powder deposition form, which restricts part-building purposes whereas remaining appropriate for coating work. “Presently, we now have little management over the form of deposition of the powder. This isn’t a difficulty for coatings however presents a major restraint for part-building purposes. Our subsequent objective is to discover a resolution to this limitation, and we have already got some very promising outcomes,” stated O’Neill.
Supply: eng.cam.ac.uk