Need to converse at AMA: Vitality 2025 or AMA: Automotive & Mobility 2025? Submit your software now!
The US Division of Vitality (DoE)’s Oak Ridge Nationwide Laboratory (ORNL) has accomplished profitable testing of two 3D printed stainless-steel capsules within the Excessive Flux Isotope Reactor (HFIR).
Supported by the DoE’s Workplace of Nuclear Vitality’s Superior Supplies and Manufacturing Applied sciences program, the mission concerned fabricating the capsules at ORNL’s Manufacturing Demonstration Facility (MDF) utilizing laser powder mattress fusion (LPBF) and 316H stainless-steel.
This materials is being assessed for its suitability in nuclear environments as a result of its power at excessive temperatures, corrosion and radiation resistance, and compliance with stringent security requirements.
“As we display the reliability of those printed parts, we’re taking a look at a future the place additive manufacturing would possibly change into normal observe in producing different essential reactor components,” mentioned Ryan Dehoff, Director of the MDF at ORNL.
Additive components examined for sturdiness
As soon as fabricated, the capsules had been assembled and certified by ORNL’s Irradiation Engineering group. They had been then positioned inside HFIR, the place they underwent a month-long irradiation cycle. After testing, each capsules had been retrieved totally intact, demonstrating their structural integrity and efficiency underneath excessive situations.
These experimental capsules are designed to carry pattern supplies throughout irradiation, performing as each containment obstacles and stress vessels. HFIR’s intense neutron surroundings, among the many highest on the earth, gives researchers with the power to check supplies and fuels underneath practical reactor situations.
Historically, irradiation capsules require customized designs and specialised supplies, making the event course of each time consuming and costly. ORNL researchers are exploring additive manufacturing as a quicker, cheaper various that additionally gives higher flexibility in design.
“Additive manufacturing will broaden my group’s toolset to develop revolutionary experiments to assist this essential want,” mentioned Richard Howard, a gaggle chief within the Nuclear Vitality and Gasoline Cycle Division at ORNL.
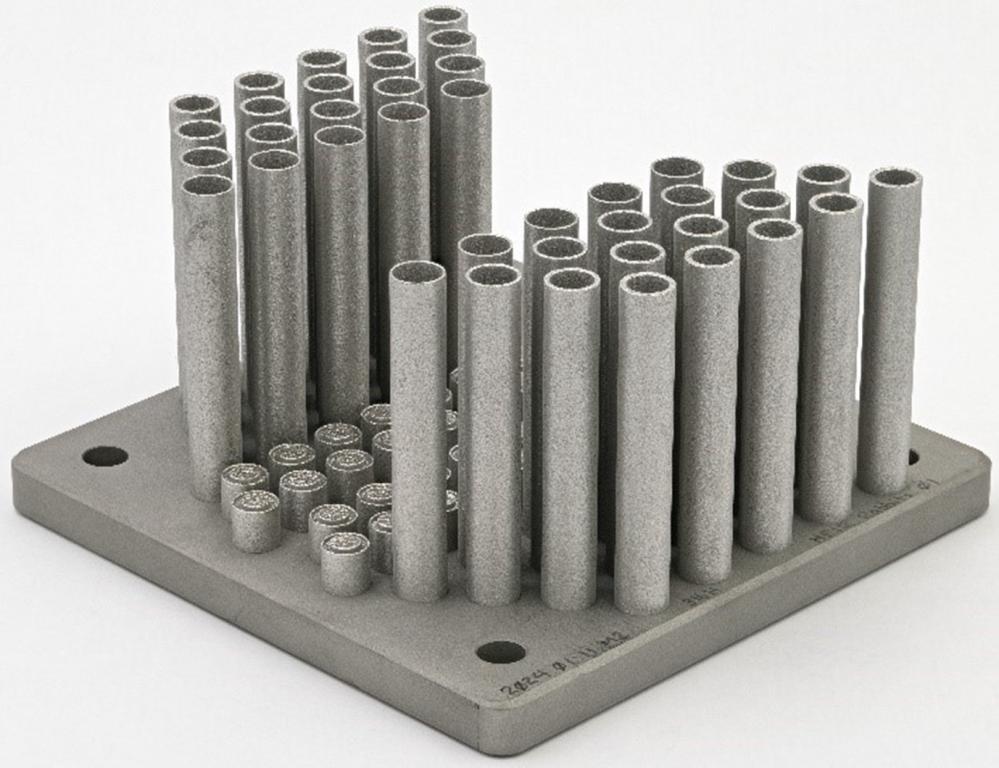
Earlier this yr, ORNL 3D printed and examined a stainless-steel rabbit capsule utilizing LPBF, marking the primary time AM was utilized to one of these nuclear part. After being assembled, sealed, and inserted into HFIR, the capsule withstood practically a month of irradiation and remained totally intact. A post-irradiation evaluation is deliberate for winter to additional consider its efficiency and potential future makes use of.
Demonstrating enhanced reactor efficiency utilizing 3D printed components
Additive manufacturing is altering how the nuclear sector designs, maintains, and helps essential gear, making the method extra adaptable, environment friendly, and dependable underneath strict regulatory requirements.
Final yr, Westinghouse Electrical Firm used 3D printing to develop a brand new filtering backside nozzle aimed toward enhancing gasoline meeting efficiency in Pressurized Water Reactors (PWRs). Built-in into 4 lead take a look at assemblies on the Joseph M. Farley Nuclear Plant, the design particularly focused particles fretting, a key contributor to gasoline rod leakage.
Having used 3D printing, engineers had been capable of create extra refined geometries that restricted the scale of particles coming into the reactor. Throughout testing, the nozzles demonstrated a 30% improve in resistance to clutter, highlighting the potential of AM to improve reactor part reliability.
Elsewhere, researchers on the Korean Atomic Vitality Analysis Institute efficiently used a mixture of 3D printing and CNC machining to supply a 30 kg safety valve to be used in a nuclear reactor. The valve featured intricate inside cooling channels and met the stringent necessities for ‘Class 1’ nuclear security classification.
What 3D printing developments must you be careful for in 2025?
How is the way forward for 3D printing shaping up?
To remain updated with the newest 3D printing information, don’t neglect to subscribe to the 3D Printing Trade publication or observe us on Twitter, or like our web page on Fb.
When you’re right here, why not subscribe to our Youtube channel? That includes dialogue, debriefs, video shorts, and webinar replays.
Featured picture reveals 3D printed stainless-steel capsules. Picture through ORNL.